- 专题资料:
- 北京科技大学
- 山东南山铝业股份有限公司
- 专题制作:
- 国家材料环境腐蚀平台
联系我们
-
-
电话: 010-62313558-802 -
地址: 北京市海淀区学院路30号 -
邮编: 100083
首页 > 舰船和海洋工程用铝合金金属腐蚀专题 > 腐蚀行为
船用铝合金腐蚀行为-室内模拟研究
1 船用铝合金在模拟海洋大气环境下的腐蚀行为研究
1.1模拟海洋大气腐蚀试验方法
室内模拟海洋大气腐蚀的主要试验方法包括湿热试验、盐雾试验、周浸试验和多因子循环复合腐蚀试验。
室内模拟海洋大气腐蚀的主要试验方法包括湿热试验、盐雾试验、周浸试验和多因子循环复合腐蚀试验。 罗雪等[1]采用质量分数为5%、pH为6.5~7.2的中性NaCl溶液进行喷雾,通过盐雾模拟海洋大气环境研究腐蚀产物对6061铝合金海洋大气腐蚀过程中的影响。罗兰等[2]分析了不同盐雾试验方法标准对盐溶液配制、试样的处理和检测、试验参数、试验过程控制等方面的不同要求,探讨了盐雾试验的操作技术,提出了必须严格控制盐雾试验过程的建议和不能用不同标准进行的盐雾试验结果进行比较的观点。但方法与大气曝晒试验无直相关性,试验盐雾无法与实际大气环境建立准确的等效关系,对户外大气腐蚀性的模拟没有针对性,因此,盐雾试验方法仅能作为一种人工加速腐蚀试验方法,对金属材料进行性能试验,不能对材料在某一实际使用环境下的寿命进行预测,但作为一种经典的加速试验方法还是具有一定意义的,主要用来模拟海洋环境(如Cl-)对材料的腐蚀。方晓祖等[3]采用循环盐雾试验箱和浸渍箱进行循环加速试验,以此7A52铝合金在万宁的海洋大气环境下的腐蚀进行室内加速模拟,h,其循环步骤如下:盐雾(5% NaCl, 35 ℃, 6 h) →干燥(60 ℃, < 35 RH, 3 h) →湿热(60 × ℃, > 95 RH,6 h) →干燥( 60 ℃, < 35 RH,3 h) →浸渍( 25 ℃,6 h,溶液) →冲洗,这种室内加速方法与7A52铝合金在万宁标准场海洋大气环境试验具有较好的相关关系。刘明等[4]采用连续盐雾、循环盐雾、周期浸泡、周期降雨等四种模式的加速腐蚀试验方法模拟2A12铝合金在海洋性大气环境中的腐蚀规律,结果表明,与连续盐雾试验、循环盐雾试验和周期浸泡试验相比,周期降雨试验能够更好地模拟2A12铝合金在琼海大气腐蚀的形貌特征;与连续盐雾试验和周期浸泡试验相比,循环盐雾试验和周期降雨试验能够更好地模拟2A12铝合金在琼海大气腐蚀的动力学规律;四种加速腐蚀试验中,整体加速性由强到弱的顺序为:循环盐雾试验,周期降雨试验,周期浸泡试验,连续盐雾试验。 综上,湿热试验只考虑了温湿度的影响,盐雾试验除温湿度外还考虑了盐粒子的影响,但该方法与大气曝晒试验无直相关性,试验盐雾无法与实际大气环境建立准确的等效关系,对户外大气腐蚀性的模拟没有针对性,仅能作为一种人工加速腐蚀试验方法;周浸试验则相对抓住了材料大气腐蚀的基本特点来研究材料海洋大气的腐蚀行为,但与实际大气腐蚀结果与溶液加速腐蚀结果仍存在一定差异;多因子循环试验除了考虑大气腐蚀的基本特点,也加入了其它主要的影响因子,最真实的再现了实际自然环境的情况。但是多因子循环试验操作过程复杂、周期长、成本较周浸试验高,且每次循环的重复性也较难保证,实际应用时的循环单元和过程设计需结合实际大气环境因素才能具备较好的模拟性。
1.2船用铝合金在模拟工业海洋大气环境下的腐蚀行为
本部分以6061铝合金为研究对象,通过在模拟工业海洋大气环境下进行室内周期浸润实验以及紫外辐照加速老化实验,并应用相应的测试分析方法,研究揭示该材料在工业海洋大气环境中的腐蚀特性及机理[5]。
本试验通过紫外辐照老化试验和周期浸润腐蚀试验模拟工业海洋大气环境,以紫外辐照一次加周期浸润一次为一个循环周期。具体试验时间和试验条件如下:
(1)紫外辐照试验。照射时间:59h;环境条件:辐照强度口=60±10W/m2,温度T=55±10℃。
(2)周期浸润试验。试验时间:48h;环境条件:温度T=40℃,相对湿度RH=90%; 腐蚀溶液:5wt% NaCl+0.25wt% Na2S2O8的混合溶液(稀硫酸调整pH=4);浸润周期:30min,其中7.5min浸润,22.5min烘烤。
试验共进行8个周期,在第2、4、6、8周期分别取出1片平板样、3片拉伸样。平板样用于形貌及成分分析。
1.2.2腐蚀形貌及腐蚀产物分析
图1为6061铝合金在模拟工业海洋大气环境不同试验周期下的宏观形貌。可以看出6061铝合金在不同周期发生了不同程度的点腐蚀,表面生成了灰白色腐蚀产物,较为均匀地附着于变为淡黄褐色的基底上,之后随着腐蚀的加剧,点蚀坑直径扩大,密度变高,灰白色腐蚀产物增多,并转变为灰褐色,到第8周期腐蚀产物基本覆盖整个基材表面,金属光泽消失。
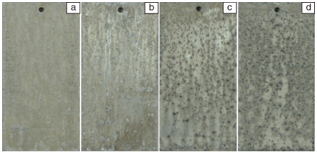
图1 6061铝合金在不同加速周期下的宏观腐蚀形貌:(a)第2周期,(b)第4周期,(c)第6周期,(d)第8周期
选取局部区域进行腐蚀微观形貌观察,结果如图2所示,6061铝合金的腐蚀是从局部点蚀开始,腐蚀点逐渐增多,并逐渐发展为小片状腐蚀区域,形成龟裂状腐蚀产物,并逐渐覆盖整个试样表面。随着腐蚀进一步加深,片层状腐蚀区域变细变多,出现堆积,由于内应力,局部区域层片开始脱落,并再次形成龟裂区,随着层片的细化,表面开始出现团絮状腐蚀产物,试样表面产物出现分层现象。该层腐蚀产物十分疏松,且有裂纹。
图3为去除腐蚀产物后试样表面形貌。6061铝合金腐蚀初期局部区域出现不规则溃疡状蚀坑,随腐蚀时间增长,腐蚀区域无规则地沿纵向和横向扩展,连接成片,局部区域有片层状剥落的现象。
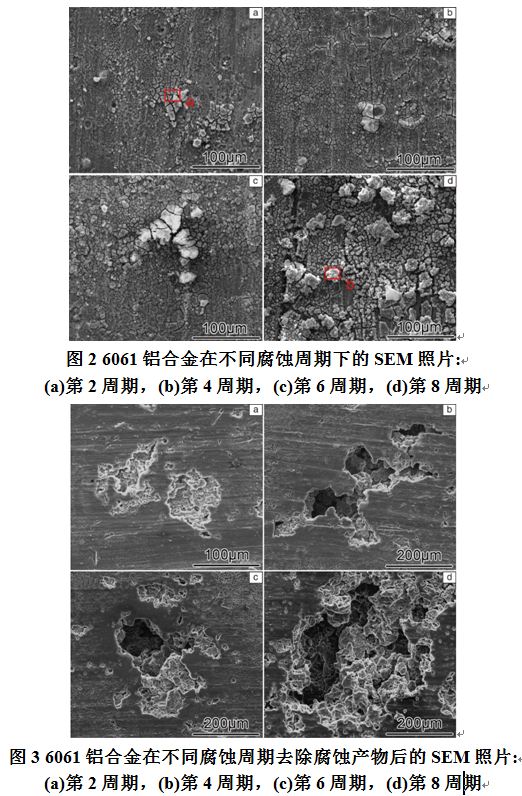
图4为6061铝合金在模拟工业一海洋环境下的腐蚀产物(图2中所示)的EDS能谱分析结果。由图4可知,6061铝合金表面的腐蚀产物主要由Al,O和S组成,具体的元素含量列于表1中。图5为6061铝合金表面腐蚀产物的红外光谱和XRD谱。结合EDS分析结果可知,腐蚀产物由经基氧化铝、硫酸铝以及氯化物组成。
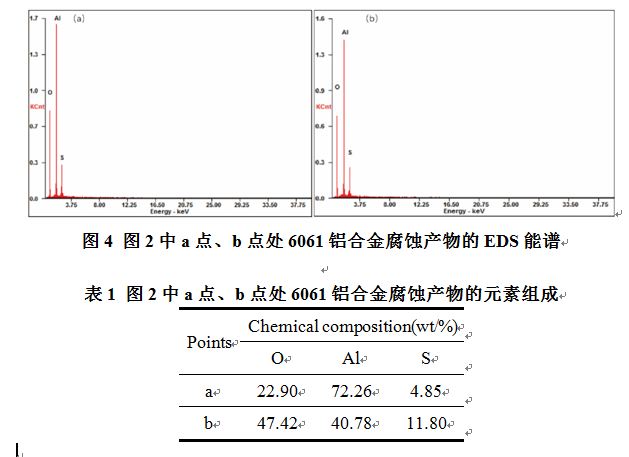
以上结果表明,6061铝合金的主要腐蚀形式为点蚀,在模拟工业海洋环境中Cl-对铝合金点蚀的加速作用主要体现在其对氧化膜的破坏上;暴露于空气中的6061铝合金试样在表面自然形成一层薄的致密的氧化膜,之后在氧化膜的表面逐渐生成AlO(OH)或Al(OH)3。工业海洋环境中的Cl-会在氧化膜中的缺陷处发生吸附并与氧化膜中的阳离子(Al3+)结合形成可溶性化合物AlCl3,即为蚀坑核。由于可溶性化合物AlCl3易发生水解,又由于该环境为酸性环境,进而溶解部分氧化膜,产生多余金属离子(Al3+)。为了维持坑内溶液电中性,外部侵蚀性离子不断向内迁移,又进一步促进水解反应,如此循环,蚀坑长大。
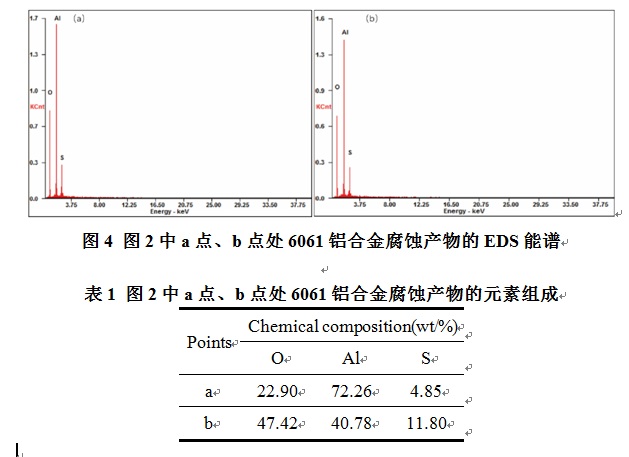
1.2.3腐蚀截面分析
图6为6061铝合金经过不同腐蚀周期后的腐蚀截面形貌。由图6可知,各试样表面均有一定厚度的锈层,可清晰地观察到腐蚀沿晶界走向延伸,表明各试样均发生了沿晶腐蚀,并且沿晶分布的腐蚀产物随着腐蚀周期的增加向晶胞内部横向扩展的趋势明显。其中试验6周后,沿晶裂纹从试样表面向内部扩展至50μm深处,8周期后沿晶裂纹最深达到80μm。随着沿晶腐蚀的加重,晶界附近形成大量质地疏松的腐蚀产物,当一个发生严重晶间腐蚀的晶胞正好处于试样表面时,整个晶粒可能会从试样表面脱落,发生剥蚀。
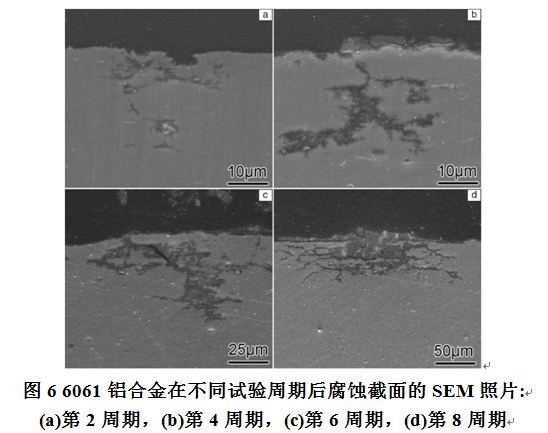
为了进一步探究腐蚀区域元素分布,对6061铝合金腐蚀试验8周期后试样的截面作电子探针显微分析(EPMA),结果如图7所示。对于6061铝合金来说,主要形成的杂质相为Al-Fe-Si和Mg2Si相。AI-Fe-Si相的电位约为-200mV,远远高于基体的电位,作为阴极相存在;Mg2Si相的电位约为-1200mV,远低于基体的电位,充当阳极,当有合适的腐蚀介质时,这些第二相与铝合金基体均构成微电偶,继而引发沿晶腐蚀。由图7b和7c发现,6061铝合金腐蚀产物中均含有大量Al和O两种元素,并且在图7c中发现O元素在表面的腐蚀产物中含量相比沿晶腐蚀产物中稍高。图7d为S元素分布,结合Al和O的元素分布发现,S在表面腐蚀产物中分布明显,在对应的沿晶腐蚀区域也能观察到S元素的聚集,说明模拟工业海洋大气环境中的硫化物不仅对试样表面的点蚀产生了很大的影响,对铝合金的沿晶腐蚀也有一定影响,主要是当硫化物溶于薄液膜形成硫酸根离子,随着腐蚀介质深入到晶界区域,为晶界区的微电偶腐蚀提供了有利的腐蚀介质,加速沿晶腐蚀的进行。
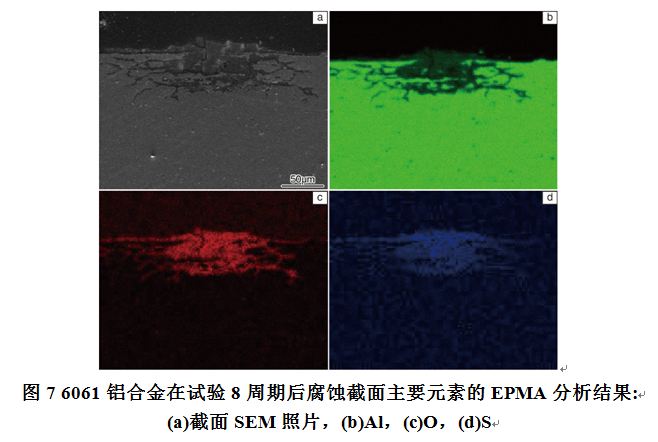
2 船用铝合金在模拟行浪花飞溅区的腐蚀行为研究
2.1 模拟飞溅区腐蚀试验方法
目前国内外尚无飞溅带腐蚀试验和防护的标准,也未有一套完整的、成熟可靠的解决方法,研究人员一般通过设计模拟海洋飞溅区试验装置来对飞溅区的腐蚀进行实验室的模拟试验。
郭晓军等[6]设计了一种工作方式的模拟海洋飞溅区试验装置,如图所示。该设备利用电动机带动搅拌转子以形成水的飞溅;通过调整电机的转速控制水的飞溅程度,来模拟海洋飞溅区波浪的大小;用气泵把空气注入水中调节水中溶氧量。利用热电偶控温调节水温,通过加热装置促使材料的加速腐蚀。并定期补加蒸馏水,以保持水中含盐量。搅拌转子的转杆与拌叶成90°,这样可在小转速下得到较大的飞溅程度。气孔处于水下左右两侧,用一小的气泵将空气注入水中,在不停搅拌下使得含氧量一致,从而调节飞溅区海水的溶氧量。容器中有加热装置调节水温,控制实验环境温度,水温最高可达80℃,可作加速腐蚀试验。通过试验,结果表明,模拟装置所得数据,与自然条件下海水对金属材料腐蚀数据基本一致,能反映现实情况,可以满足科研条件需求。
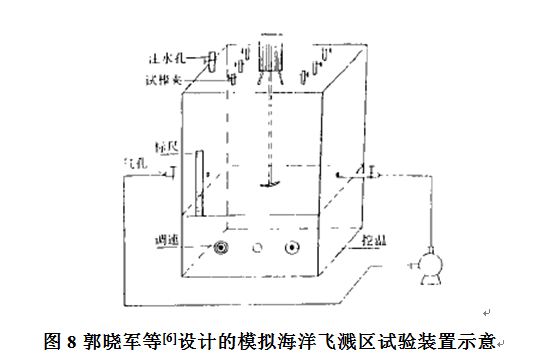
张爱萍等[7]设计一种耐候钢飞溅腐蚀试验装置,如图所示。在该实验装置中,试验时将金属材料安放于试样支架上,通过恒温装置调节海水介质温度并使其保持恒温,由水泵抽取耐腐蚀容器下部的海水介质向耐腐蚀容器内壁喷射,水流经折射形成对金属材料试样的飞溅。通过调节水泵的喷射压力和喷射方向,即可方便地改变所形成海水飞溅的形态,与通过恒温装置调节海水介质温度的手段相结合,可针对不同影响因素进行模拟。该装置能够在实验室内模拟海水运动和飞溅状态,使实验条件更加接近自然状态,故能在一个较短的时间内得到大量科学合理的试验数据,并可针对不同影响因素进行模拟,有利于缩短新品种金属材料的研究开发周期。
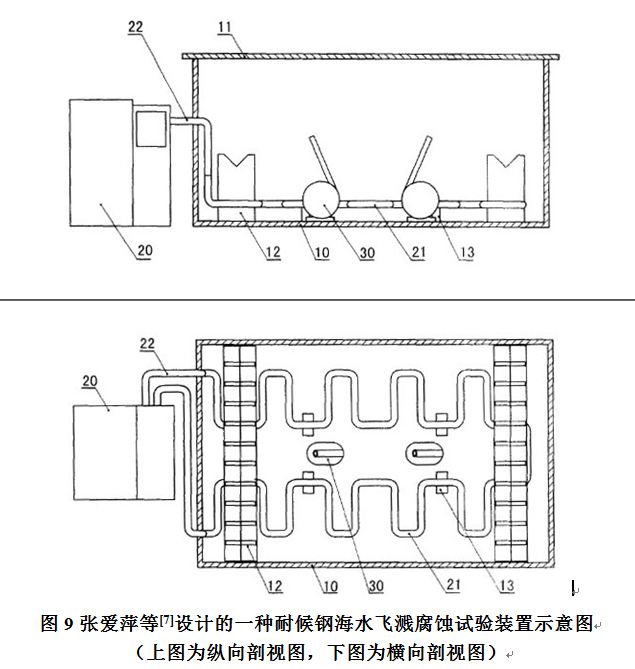
Xiang Li等[8]开发了一种包含有电化学测试系统和环境模拟腔的浪花飞溅区腐蚀模拟装置,如图所示。该装置内部一端装有三电极体系,并通过导线与箱体外部的电化学测试系统相连接,另一端安装有与水泵相通的喷嘴,可将模拟海水溶液喷洒在试样表面模拟浪花飞溅区的状态,水泵由计时器控制来实现循环定时工作。经过干湿周期循环,通过开路电位和电化学阻抗谱的测定,研究了304不锈钢的点蚀行为来测试该装置的模拟性能,结果表明经过电化学测试所显示的规律性与实际规律相符合,而且电化学测试的结果与微观观测的结果能够很好地对应。
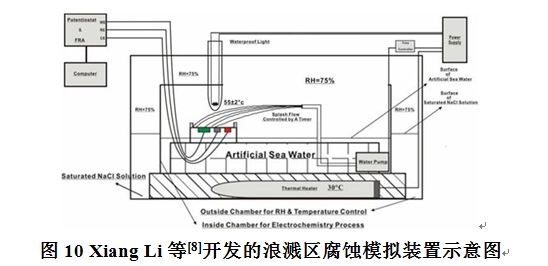
侯健等[9]发明了一种海洋飞溅环境模拟试验装置,如图示。该装置箱盒式机构的试验箱体一侧面上不制有串通式测试电缆孔,另一侧制有框架结构的传动拉杆,下部制有飞溅板角度调节杆,飞溅板角度调节杆的内端处制有飞溅板;液体区处的侧面上自上而下排列分别制有各传感器和进水口;试验箱体的顶侧面上自右向左一次排列分别固定制有气体排出口,通风排湿器、红外加热灯和箱体温度传感器;试验箱体的对应于制有传动拉杆的侧面的对向侧面处分别制有紫外灯、鼓风风机、喷头、喷水水泵、液位控制器、溶解氧传感器和排水口;其结构简单、操作方便、自动化程度较高、无需人工值守,可在实验室内模拟海洋飞溅环境,实现对材料腐蚀老化性的分析评价。
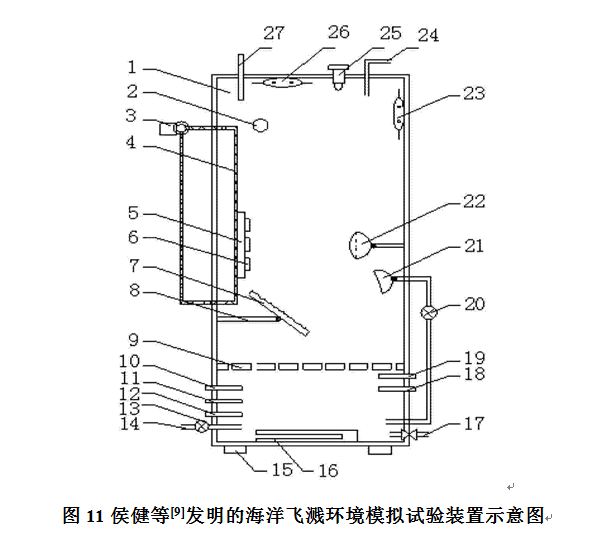
目前国内外对铝合金海洋飞溅区腐蚀模拟加速试验的研究相对较少,上述所列的飞溅试验装置,通过大量的数据验证,其工作性能基本可靠,能够基本上反映飞溅区的现实环境,得到与实际相一致的结果,为研究铝合金在海洋飞溅区的腐蚀机理,发挥着越来越重要的作用。
2.2 船用铝合金在模拟飞溅区的腐蚀行为
实验装置是在调研了目前已经公开的专利设计的海洋环境腐蚀室内模拟试验装置后,尽可能考虑多种因素的综合作用,自主设计制造的海洋腐蚀模拟加速试验装置[10],如图12所示。
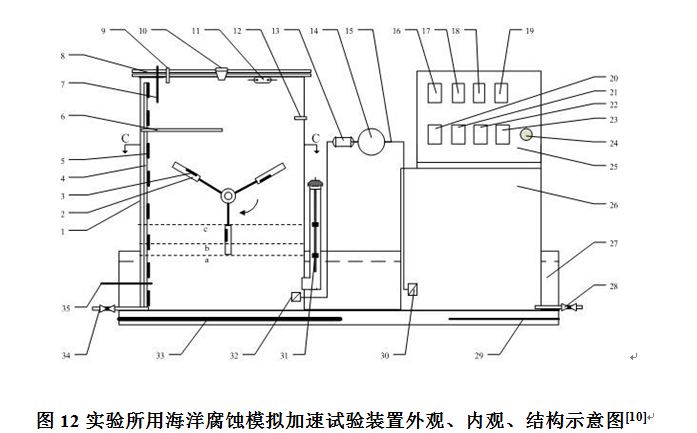
模拟加速实验装置的主工作箱和贮水箱中装有实验室配制的模拟海水溶液,主工作箱和贮水箱通过蠕动泵接通,最高水位550mm,最低水位500mm,蠕动泵转速100rpm,可控制模拟涨落潮时间约为30min。当液位处于最高时,螺旋桨开始工作,模拟浪花飞溅;当液位处于最低时,螺旋桨工作停止,热风机开始工作烘烤试样。此过程循环往复,从而达到干/湿周期交替加速腐蚀的目的。旋转试样架工作时间为10min,到时后,液位开始下降;热风机工作时间为30min,到时后,液位开始上升。实验溶液设置为:Cl-浓度为3.5%wt,NaHSO3浓度为0.01M,溶液温度为35℃,烘干温度为40℃,加速模拟严酷条件下的青岛海域实海环境,其中0.01mol/L NaHSO3是根据青岛试验站SO2日沉积量,按薄液膜厚度为100um计算而来,实验周期为5d、10d、15d、20d[11]。
2.2.1 腐蚀形貌分析
图13为5083、6061-T6铝合金污染海洋飞溅区5d、10d、15d、20d后的宏观腐蚀形貌。
可以看出腐蚀初期两种铝合金表面状态发生了明显的改变,失去了原来的金属光泽并产生了均匀分布的黑色斑点,表现为均匀腐蚀;随着时间的延长铝合金表面慢慢变得凹凸不平,颜色逐渐加深,黑色斑点逐渐长大。对比同一周期的5083-H116铝合金和6061-T6铝合金的腐蚀状态可发现,6061-T6铝合金表面初期就产生了明显的斑点,而5083-H116铝合金表面初期相对平整并未出现明显斑点;腐蚀后期6061-T6铝合金表面接近黑色,均匀分布着较大黑色斑点,而5083-H116铝合金表面颜色相对较浅,表面仅分布着一些不太明显的黑色斑点。表明模拟海洋飞溅区环境中,6061-T6铝合金的腐蚀更为严重。
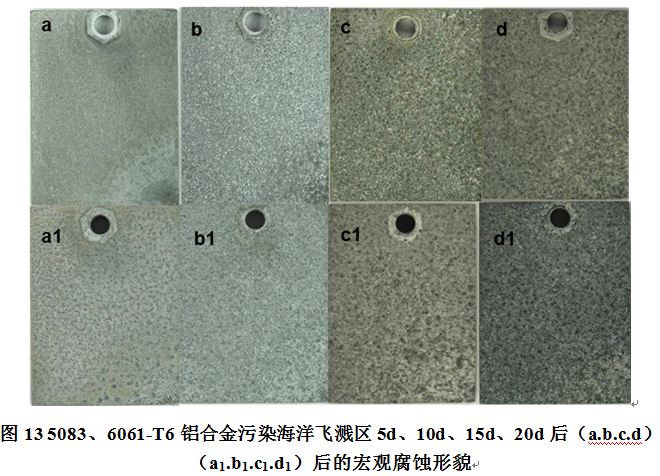
图14、15分别为5083、6061-T6铝合金污染海洋飞溅区5d、10d、15d、20d后后的微观腐蚀形貌及局部放大图。
可以看出5083-H116铝合金腐蚀后微观形貌的特点为:初期表面覆盖着一层较为致密的腐蚀产物,并分布着一些较小的点蚀坑,由局部放大图可发现点蚀坑周围分布着较多腐蚀产物,呈龟裂状;随着时间的延长,较小的点蚀坑逐渐减少并出现了较大点蚀坑,不断形成新的团状腐蚀产物并在模拟浪花的冲击下发生脱落,形成了局部较为疏松的腐蚀产物和凹凸不平的表面状态。
6061腐蚀后微观形貌的特点为:腐蚀初期已产生较大点蚀坑,点蚀坑周围分布着较多腐蚀产物,呈龟裂状。随着时间的延长,块状腐蚀产物逐渐增多,在模拟浪花的冲击下发生脱落呈层状,产生新的点蚀坑和新的裂纹。
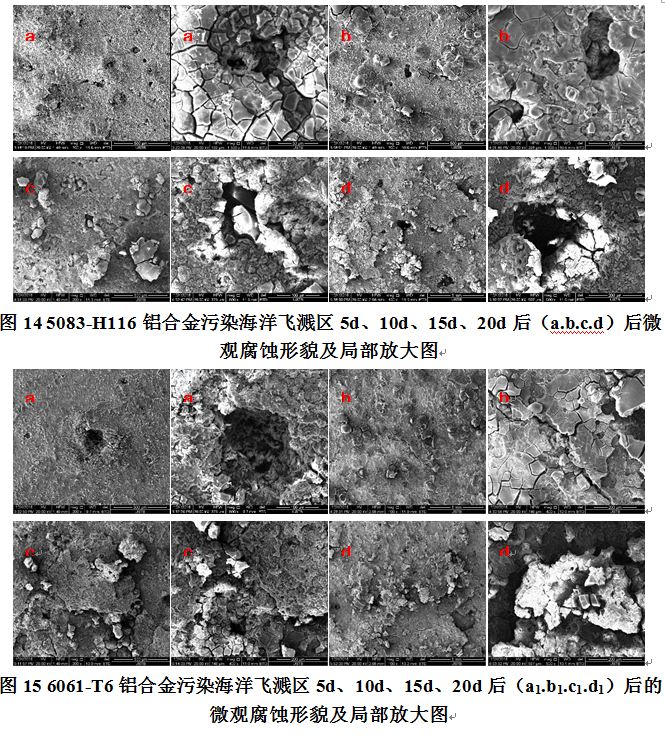
2.2.2 去除腐蚀产物后形貌分析
图16为5083-H116铝合金污染海洋飞溅区5d、10d、15d、20d后去除腐蚀产物的形貌和3d图像。可以看出腐蚀初期点蚀坑几乎均匀密布在整个基体表面,局部区域分布着一些较大点蚀坑;随着时间的延长,较大点蚀坑逐渐增多并与相邻近点蚀坑发生融合成为更大的点蚀坑。
图17为6061-T6铝合金污染海洋飞溅区5d、10d、15d、20d后去除腐蚀产物的形貌和3d图像。可以看出6061-T6铝合金初期已产生了很大的点蚀坑;随着时间的延长,较大点蚀坑逐渐与周围点蚀坑发生融合、长大,后期铝合金表面基本完全遭到破坏,只剩下小面积的基体未受到侵蚀。
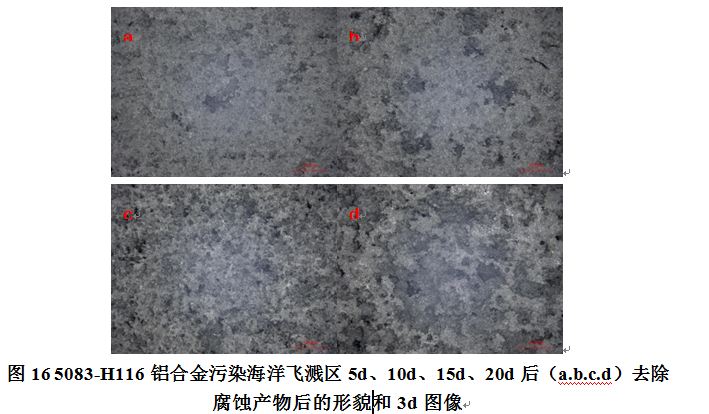
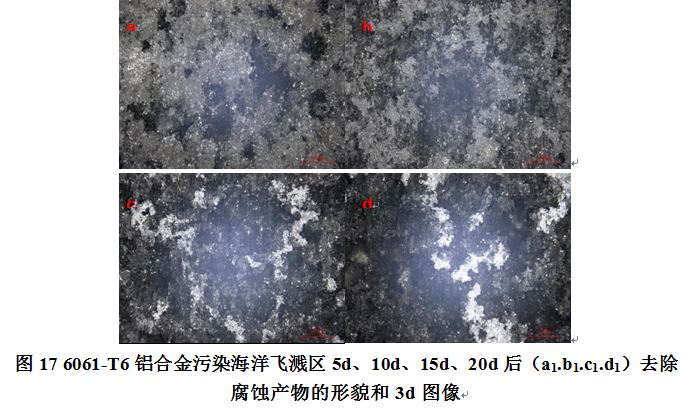
2.2.3腐蚀动力学规律
5083-H116铝合金和6061-T6铝合金在模拟污染海洋飞溅区的腐蚀数据见表2,失重曲线见图18,腐蚀速率曲线见图19。可以看出,在模拟污染海洋飞溅区环境中,随着时间延长,两种铝合金的腐蚀坑深度逐渐增加,且同一周期两种铝合金腐蚀坑最大深度相差不大;由失重曲线可看出,两种铝合金在模拟污染海洋飞溅区的失重曲线大致相似,表明其腐蚀规律大致相同,随着时间的延长,腐蚀速率先减小后增大,可能是因为腐蚀中期铝合金表面腐蚀产物对的增多对基体起到了一定保护作用,腐蚀后期由于模拟海浪的冲击作用使腐蚀产物脱落而疏松开裂,继而又加深了腐蚀作用。
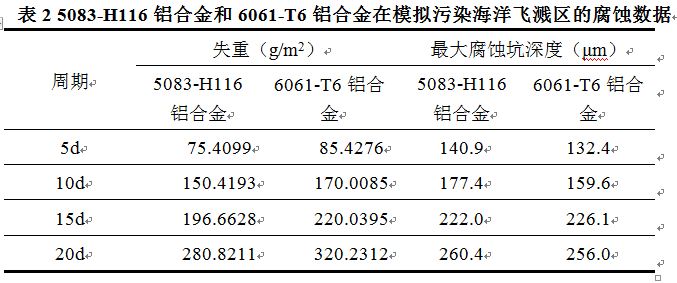
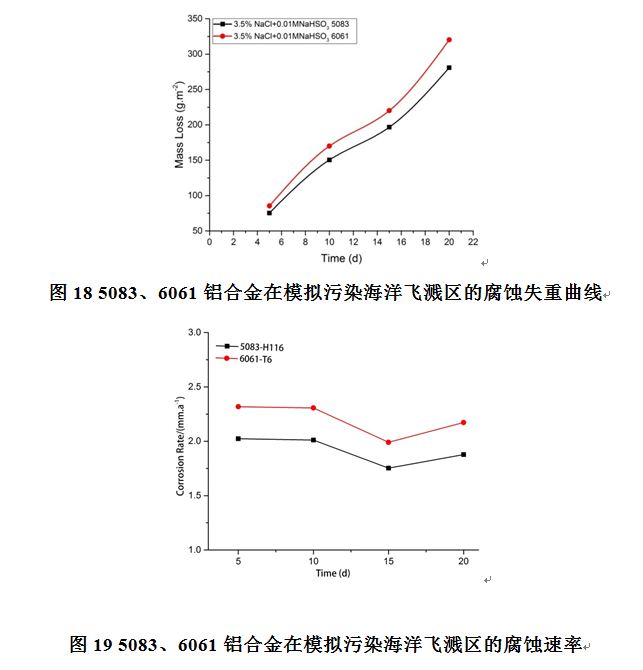
3船用铝合金在模拟潮差区的腐蚀行为研究
3.1模拟潮差区腐蚀试验方法
目前对潮差区腐蚀的实验室模拟主要通过自主设计的试验装置、通过周期性试验来模拟潮差区的潮涨潮落带来的腐蚀效应,试验过程设计需考虑实际被模拟的海水及当地环境因素等才能取得较好的模拟效果。
穆鑫等[12]在自制试验槽内通过控制模拟海水(含3.33%海水晶的水溶液)在试验槽的水位高度周期性变化来模拟潮差区的海水涨落过程,研究了低碳钢在该潮差区模拟条件下的腐蚀行为。
3.2船用铝合金在模拟潮差区的腐蚀行为
本节通过设置3.5%wt NaCl溶液以及在3.5%NaCl溶液中添加0.02M的NaHSO3两种溶液,来模拟海洋大气环境和工业海洋大气环境进行干湿周浸实验,考察船用铝合金在工业、非工业海洋大气环境中不同周期后的腐蚀行为[11]。
实验按照国标GB/T 19746-2005《金属和合金的腐蚀盐溶液周浸实验》在干湿周浸实验箱中进行,为了更好地实现加速腐蚀,进行折算时一般将加速试验环境设置的较为苛责,以尽量缩短实验时间,提高腐蚀效率。干湿周浸实验中采用3.5%NaCl溶液来模拟海洋大气环境,采用3.5%NaCl+0.02MNaHSO3溶液来模拟工业海洋大气环境,两种模拟液均调整为PH≈4;两种模拟液均以60min为一个循环周期:15 min浸润和45 min干燥。溶液温度为(40±1)℃,箱内空气温度设定为(40±1)℃。失重实验样品取样周期为2d、4d、8d、15d、25d、35d。
3.2.1腐蚀形貌及产物分析
图20为5083、6061-T6铝合金在3.5%NaCl、3.5%NaCl+0.02MNaHSO3模拟溶液中,周浸实验进行周期分别为2d、4d、8d、15d、25d、35d样品表面除锈前宏观形貌。
可以看出,在NaCl模拟液中周浸2d后两种铝合金表面均出现很小的黑色点蚀坑,但6061-T6铝合金肉眼可见黑色点蚀坑要多于5083-H116铝合金;4d后,两种铝合金腐蚀坑数量迅速增加,5083-H116铝合金点蚀坑分布具有一定方向性,而6061-T6铝合金腐蚀坑发生了一定程度的增大并出现了白色腐蚀产物;8d后,5083-H116铝合金点蚀坑呈“条带状”分布,并出现少量腐蚀产物,6061-T6铝合金点蚀坑明显增大,数量增加,相邻近的点蚀坑有融合的趋势;15d后,两种铝合金均出现明显的白色腐蚀产物,基本覆盖了黑色点蚀坑,5083-H116铝合金点蚀坑明显增大,6061-T6铝合金点蚀坑数量明显多于5083-H116铝合金,几乎完全覆盖了基体表面;25d后,5083-H116铝合金带有白色腐蚀产物的点蚀坑继续增多、增大,部分较大的团状白色腐蚀产物包含了两个黑色点蚀坑,表明此时相邻近的点蚀坑已经发生了融合,6061-T6铝合金表面继续产生了更多的黑色点蚀坑并且相邻近的点蚀坑发生了融合扩大,并由点蚀发展成局部腐蚀;35d后,白色腐蚀产物基本覆盖了两种铝合金原来的黑色点蚀坑并且继续长大,5083-H116铝合金点蚀基本覆盖表面且已发生了局部腐蚀,而6061-T6铝合金几乎已发展为均匀腐蚀,腐蚀产物分布相比5083-H116铝合金更为密集。
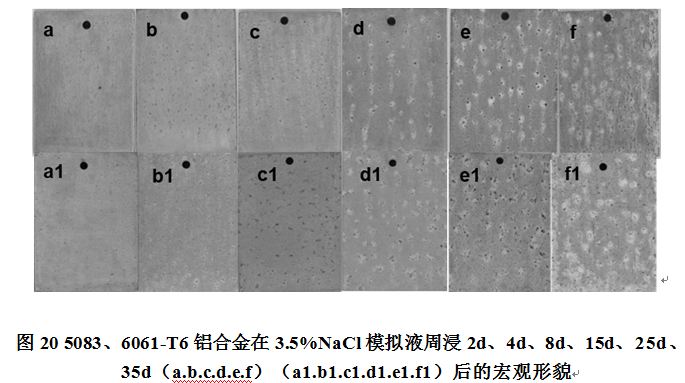
从图21可以看出,在3.5%NaCl+0.02MNaHSO3模拟溶液中周浸2d后,两种铝合金表面状态发生了明显改变,出现了“花斑状”腐蚀形貌,5083-H116铝合金表面几乎没有点蚀坑的出现,而6061-T6铝合金表面产生了部分黑色点蚀坑;4d后,5083-H116铝合金表面出现少量点蚀坑,周围分布着少许白色腐蚀产物,6061-T6铝合金黑色点蚀坑数量继续增加且明显高于5083-H116铝合金;8d后,5083-H116铝合金腐蚀坑数量增加,白色团状腐蚀产物增大,6061-T6铝合金黑色点蚀坑分布基本覆盖基体表面;15d后,5083-H116铝合金白色团状腐蚀产物继续扩大且数量增加,并有新的黑色点蚀坑的产生;6061-T6铝合金黑色点蚀坑周围开始出现白色腐蚀产物;25d、35d后5083-H116铝合金白色团状腐蚀产物数量继续增加,面积继续扩大直至均匀分布整个基体表面,没有发生局部腐蚀,6061-T6铝合金表面带有少量白色腐蚀产物的黑色点蚀坑数量继续增加,并发生了局部腐蚀,后期白色团状腐蚀产物开始聚积,并在周围密布着黑色点蚀坑。
综上,对比两种铝合金不同周期的宏观腐蚀形貌我们可以发现,就点蚀坑的数量和分布而言,同一周期5083-H116铝合金腐蚀程度总是低于6061-T6铝合金;对于同一种铝合金,同一周期后含HSO3-环境下的腐蚀程度均高于不含HSO3-的环境,表现为腐蚀坑的增多、增大、腐蚀产物的增加;两种铝合金腐蚀规律均为点蚀的萌生、长大、数量增加,直至均匀分布在整个基体表面,发展为局部腐蚀。
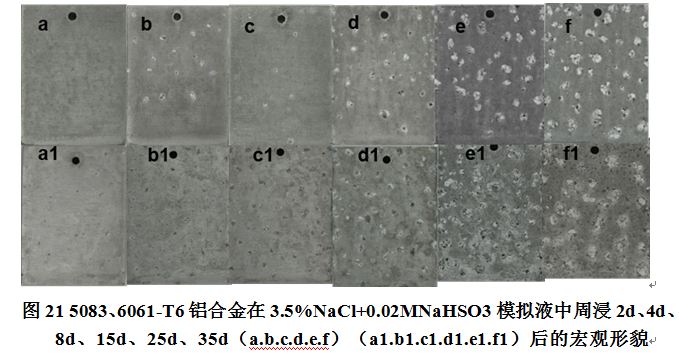
图22、23、24、25、26、27为5083、6061-T6铝合金在3.5%NaCl、3.5%NaCl+0.02MNaHSO3模拟溶液中周浸实验进行周期分别为2d、4d、8d、15d、25d、35d后除锈前的SEM微观形貌。从图22可以看出,图a表示腐蚀初期5083-H116铝合金产生了几十微米大小的点蚀坑,分布具有一定方向性,这些点蚀坑的出现可能与铝合金表面第二相的脱落有关,点蚀坑周围有少量腐蚀产物,表面氧化膜基本完整;图b表示6061-T6铝合金已产生较大的团状腐蚀产物,周围钝化膜受到破坏,说明在Cl-的作用下钝化膜薄弱部位发生了局部破坏和活化,发生铝的溶解,其腐蚀微电池模型可表示为:中心的第二相作为阴极,周围裸露基材作为阳极,而最外部钝化膜由于电位相对于裸露基材较正,作为阴极;图a1表示腐蚀初期5083-H116铝合金产生了连续的具有方向性的微小腐蚀坑,局部氧化膜发生皲裂、脱落,裸露出铝合金基材;从图b1看出6061-T6铝合金已产生较大团状腐蚀产物,发生了较为严重的点蚀。
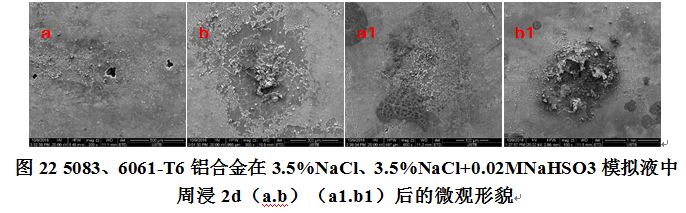
之后在模拟海洋大气环境中,5083-H116铝合金腐蚀产物不断增多,8d后基本覆盖原来的点蚀坑,腐蚀产物由于内应力作用发生龟裂,呈现块状或粒状,分布呈条带状;随着时间的延长,腐蚀产物以某一点为中心不断聚积、长大成扁长的椭圆形,而腐蚀产物表面裂纹也逐渐增大直至边缘和表面的部分腐蚀产物脱落;6061-T6铝合金腐蚀产物的变化也呈现相似的规律,不同的是腐蚀产物的形状接近圆形,同一周期腐蚀产物的面积也大于5083-H116铝合金。
之后在模拟工业海洋大气环境中,5083-H116铝合金和6061-T6铝合金腐蚀产物形状接近圆形,发展规律均为腐蚀产物以某一点为中心不断聚积、长大,最后成为层状带有裂纹的疏松腐蚀产物结构,表现为典型的点蚀特征;对比同一周期的腐蚀形貌可以发现,5083-H116铝合金腐蚀产物面积总是小于6061-T6铝合金,同一材料同一周期后,模拟工业海洋大气环境下铝合金的腐蚀产物面积大于模拟海洋大气环境下铝合金的腐蚀坑面积。
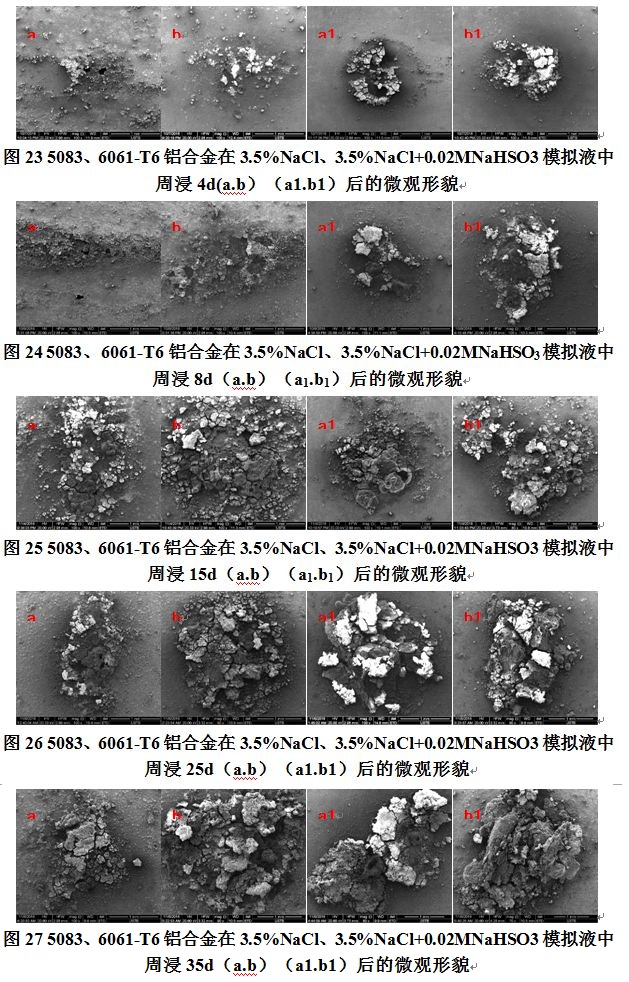
图28和表3为两种模拟溶液周浸35d后,5083、6061-T6铝合金表面腐蚀产物的EDS结果。

可以看出,腐蚀产物中铝元素质量分数最高,其次是O、S和微量Cl元素,可见两种模拟液中,5083-H116铝合金和6061-T6铝合金腐蚀产物主要为铝的氧化物,O元素和Al元素的比例大致相似,也说明两种铝合金在不同模拟液中的腐蚀产物结构相似。
铝合金在大气中的一般反应为

在模拟海洋大气环境中,Cl-首先在铝表面第二相部位或者氧化膜缺陷处发生吸附,进而与氧化膜发生反应,导致氧化膜减薄和铝合金基材的溶解;其腐蚀机制可表示为:

模拟工业海洋大气环境中,薄液膜内HSO3-和Cl-的协同作用下,铝合金发生更为严重的腐蚀,腐蚀产物为铝的氧化物和铝的硫酸盐水合物,其腐蚀机制为:

3.2.2 腐蚀动力学规律
5083-H116铝合金和6061-T6铝合金在模拟液中周浸腐蚀数据见表4、5,失重曲线见图29,腐蚀速率曲线见图30。
从表4、5可以看出,在不同模拟液中,随着时间的延长,两种铝合金的腐蚀坑深度逐渐增加,且同一周期两种铝合金腐蚀坑最大深度相差不大;对于同一种铝合金,同一周期3.5%NaCl+0.02MNaHSO3模拟液中最大腐蚀坑深度明显大于3.5%NaCl模拟液中最大腐蚀坑深度,表明NaHSO3的加入促进了点蚀过程。
从图29、30可以看出,两种铝合金在不同模拟液中的失重曲线和腐蚀速率曲线大致相似,表明其腐蚀规律大致相同,腐蚀速率先增大后减小,腐蚀速率曲线呈M形,表明前期为加速腐蚀阶段,中期由于腐蚀产物的增加覆盖在基体表面,形成了一定保护作用,进一步腐蚀产物疏松开裂,侵蚀性离子容易达到基体促进腐蚀,之后新的腐蚀产物的形成又会对腐蚀产生一定抑制作用;对于同一种铝合金,NaHSO3的加入明显加速了腐蚀,且NaHSO3的加入对6061-T6铝合金腐蚀的加速作用要大于5083-H116铝合金,可见6061-T6铝合金对NaHSO3有着更高的腐蚀敏感性。
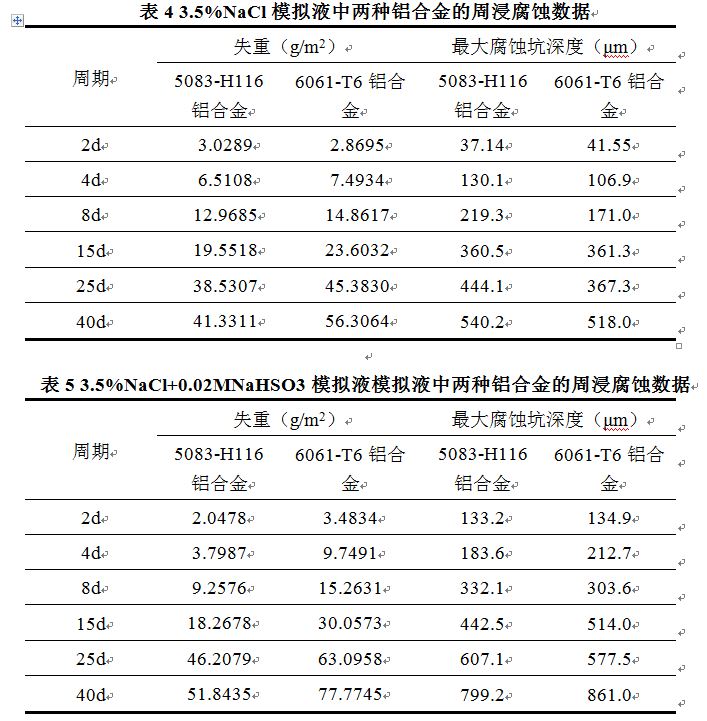

4船用铝合金在模拟全浸区的腐蚀行为研究
4.1模拟全浸区腐蚀试验方法
海水全浸区腐蚀的试验室模拟主要通过浸泡试验来开展,试验介质为天然海水或配制的含NaCl的模拟溶液,包含静态海水试验和动态海水试验。其中:静态海水浸泡试验仅考虑腐蚀性海水介质的腐蚀作用,较为简易;而动态海水试验进一步考虑了海水的冲刷运动等作用,更能模拟海水流动带来的综合腐蚀破坏效应,模拟过程也更复杂。
韩东锐等[13]采用青岛海域海水作为介质开展了室内海水浸泡试验,通过室内模拟全浸区腐蚀作用来研究不同表面处理工艺对6061铝合金的耐海水腐蚀性能的影响。彭文才等[14]选取青岛天然海水作为试验介质来模拟海水环境,研究了温度和溶解氧对5083铝合金海水腐蚀性的影响。王勇等[15]采用不同浓度的NaCl溶液作为海水模拟介质来研究究7005和5052铝合金在模拟海水介质中的耐腐蚀性。刘雪琴[16]采用多种组分模拟海水介质,研究了5383铝合金在不同流速的模拟海水介质中的腐蚀行为,发现5383铝合金的耐蚀性随着海水流速的增大而增强。
4.2船用铝合金模拟海水浸泡腐蚀行为
海洋环境腐蚀影响因素较多,本小节主要研究Cl-浓度、温度、SO2含量等不同因素环境下5083-H116铝合金和6061-T6铝合金的腐蚀行为,分析其腐蚀电化学规律和腐蚀形貌。
为考察单一因素对铝合金极化曲线规律的影响,通过电化学手段研究材料腐蚀趋势,设置如下不同参数的测试溶液:模拟溶液的NaCl浓度(质量分数)分别为1%、2%、3.5%、5%、7%,测试的温度为室温;模拟溶液采用质量分数为3.5%的NaCl溶液,测试温度分别为室温、35℃、45℃、50℃、55℃、65℃;模拟溶液采用质量分数为3.5%的NaCl溶液,添加浓度分别为0M,0.005M,0.01M, 0.02M,0.05M的亚硫酸氢钠,测试的温度为室温。
为进一步研究不同因素对铝合金腐蚀行为的影响,本节采用了化学浸泡法,研究两种铝合金在不同环境下的溶液中浸泡30d后的腐蚀行为,溶液采用GB/T 19746- 2005《金属和合金的腐蚀盐溶液周浸实验》配制的模拟海水溶液分别设置三种如下不同参数的浸泡溶液:三种模拟海水溶液Cl-浓度分别为3.5%、5%、7%,实验温度为室温;三种模拟海水溶液添加NaHSO3浓度分别0M、0.01M、0.02M,实验温度为室温;三种正常的海水模拟液,浸泡实验分别在室温、35℃、45℃下进行。
4.2.1动电位极化曲线分析
(1)Cl-浓度的影响
5083-H116铝合金和6061-T6铝合金在不同盐度的氯化钠溶液中的动电位极化曲线如图31所示。拟合的腐蚀电流密度Icorr和自腐蚀电位Ecorr见表6。
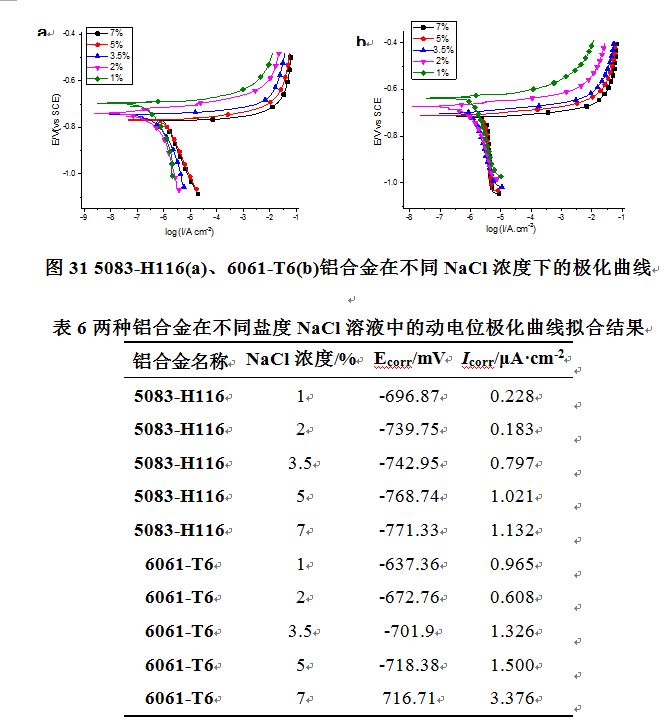
由表6可以看出,同一NaCl浓度下,5083-H116铝合金的腐蚀电流密度均小于6061-T6铝合金,说明在同一NaCl浓度下5083-H116铝合金的耐蚀性要高于6061-T6铝合金;两种铝合金1%NaCl浓度下的腐蚀电流密度略大于2%NaCl浓度的腐蚀电流密度,这可能是因为Cl-与溶解氧在铝合金表面发生了竞争吸附作用,使铝合金的腐蚀程度略微降低;之后随着Cl-浓度的增加,均出现腐蚀电流密度增大,自腐蚀电位负移的情况,而且没有出现明显的钝化现象。

随着Cl-浓度的升高,两种铝合金阳极电流不断增大,表明随着浓度的升高,活性氯的浓度也随着增加,进而对铝合金钝化膜造成更强的破坏作用,加速阳极溶解,导致腐蚀电流密度增大,随着Cl-浓度的升高,铝合金的腐蚀速率不会一直增加,在某一Cl-浓度下腐蚀速率达到最大值,之后随着Cl-浓度的增加而下降。
(2)HSO3-浓度的影响
5083-H116铝合金和6061-T6铝合金在不同盐度的氯化钠溶液中的动电位极化曲线如图32所示。拟合的腐蚀电流密度Icorr和自腐蚀电位Ecorr见表7。
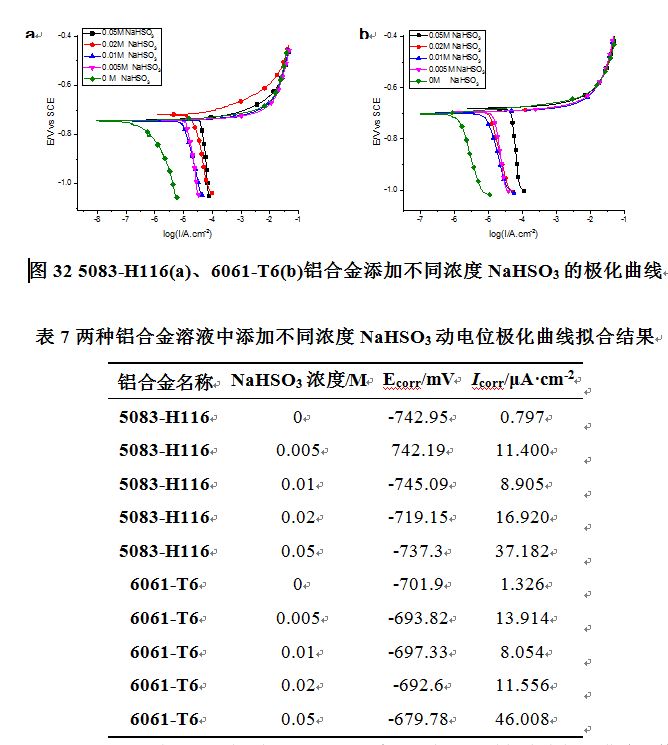
由表7可以看出,随着添加NaHSO3浓度的增加,两种铝合金极化曲线规律相似:自腐蚀电位变化很小,NaHSO3浓度的为0.005M时,两种铝合金的腐蚀电流密度迅速增大,是3.5%NaCl溶液中腐蚀电流密度的十几倍之多;随着NaHSO3浓度的继续增加,腐蚀电流密度先减小后增大,两种铝合金也未出现明显的钝化现象。这说明NaHSO3的加入使铝合金的耐蚀性大幅度降低,且浓度超过0.01M之后,两种铝合金的耐蚀性随着NaHSO3浓度的增加而降低。
HSO3-在溶液中会发生水解和电离,可用如下公式表示,其中电离作用要大于水解作用,因此HSO3-的加入使H+浓度增加,一方面使溶液变为酸性,破坏铝合金钝化膜,加速铝合金溶解,另一方面也促进了阴极析氢反应的发生。

在相同的NaHSO3浓度下,两种铝合金的腐蚀电流密度几乎均为同一个数量级,说明NaHSO3对两种铝合金耐蚀性能的影响程度相似。
(3)温度的影响
5083-H116铝合金和6061-T6铝合金在不同温度的氯化钠溶液中的动电位极化曲线如图33所示。拟合的腐蚀电流密度Icorr和自腐蚀电位Ecorr见表8。
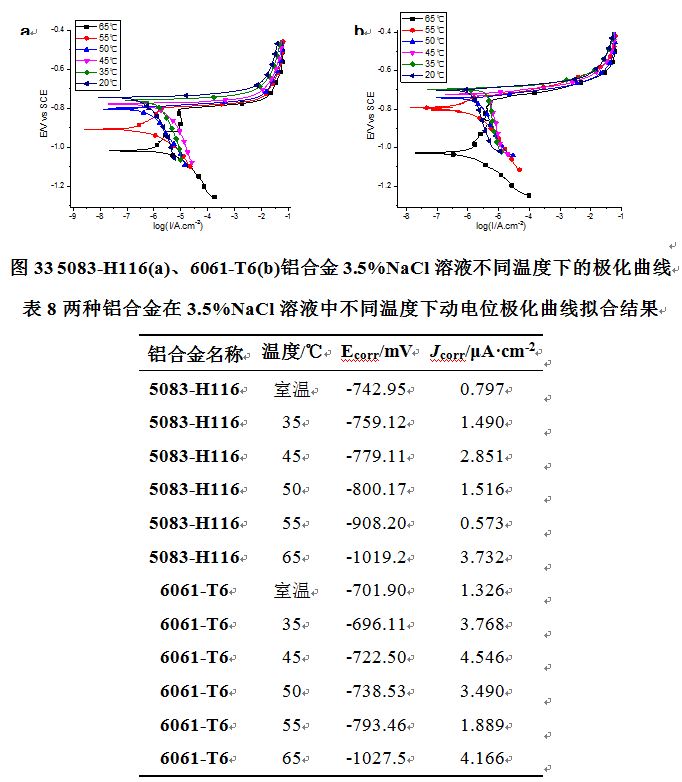
由表8可以看出两种铝合金的极化曲线规律基本相似。随着溶液温度的升高,两种铝合金的自腐蚀电位均逐渐负移;随着温度的升高,两种铝合金的的腐蚀电流密度在室温~45℃逐渐升高;一方面由于温度的升高导致化学反应的活性升高,另一方面,溶液电阻也会随着温度的升高而降低,因此两种铝合金的腐蚀速率在室温~45℃逐渐升高。
而在50℃时,两种铝合金的腐蚀电流密度开始降低;55℃时两种铝合金均出现了明显的点蚀电位,均未出现钝化平台,腐蚀电流密度继续降低;65℃时腐蚀电流密度又开始上升,并出现了不太明显的钝化平台,可推知中间某一温度可达到最低腐蚀电流密度;这主要是因为在较高温度时,铝合金更容易与溶液中的溶解氧结合,使得钝化能力增强,生成更为致密的氧化膜。在此过程中,化学反应活性的升高与铝合金钝化能力增强产生竞争现象,50℃~某一温度铝合金钝化占主导作用,某一温度~65℃化学反应活性的增强占主导作用。
同一温度下,6061-T6铝合金的腐蚀电流密度均大于5083-H116铝合金,表明在相同温度下5083-H116铝合金的耐蚀性能要高于6061-T6铝合金。
综上所述,Cl-浓度的升高能明显加速其阳极反应;HSO3-的加入能极大地促进其阴极反应,提高其腐蚀电流密度,酸性的溶液环境使铝合金钝化膜发生严重破坏,温度的升高也能明显加速铝合金的腐蚀。
4.2.2 腐蚀形貌分析
图34为两种铝合金不同温度下浸泡30d后的腐蚀形貌。对比分析可发现两种铝合金随温度的升高,腐蚀程度越来越严重,而同一温度下5083-H116铝合金的耐蚀性能要高于6061-T6铝合金。图35为两种铝合金不同Cl-浓度下浸泡30d后的腐蚀形貌,可以看出,随着Cl-浓度的增加,铝合金的腐蚀程度加深。同一Cl-浓度下5083-H116铝合金的耐蚀性仍要高于6061-T6铝合金。图36为两种铝合金不同NaHSO3浓度下浸泡30d后的腐蚀形貌,可以看出添加NaHSO3添加对铝合金的腐蚀有着显著地促进作用,而且这种促进作用随着添加NaHSO3浓度的升高而加强。
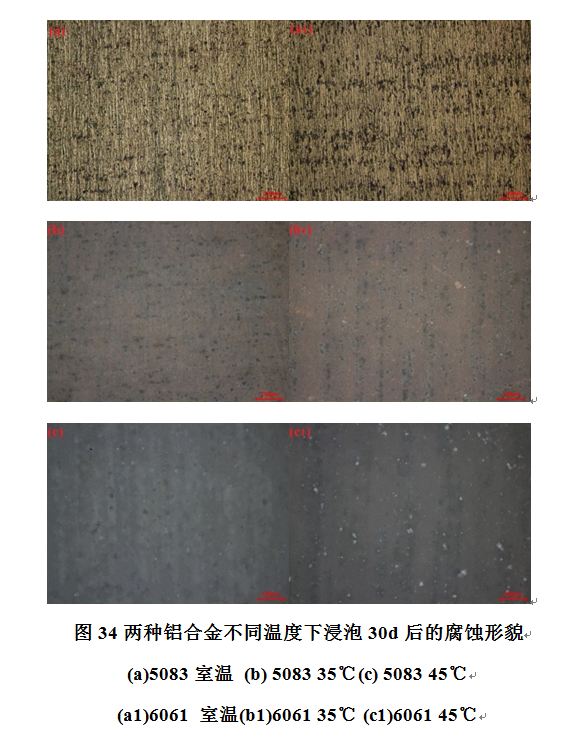
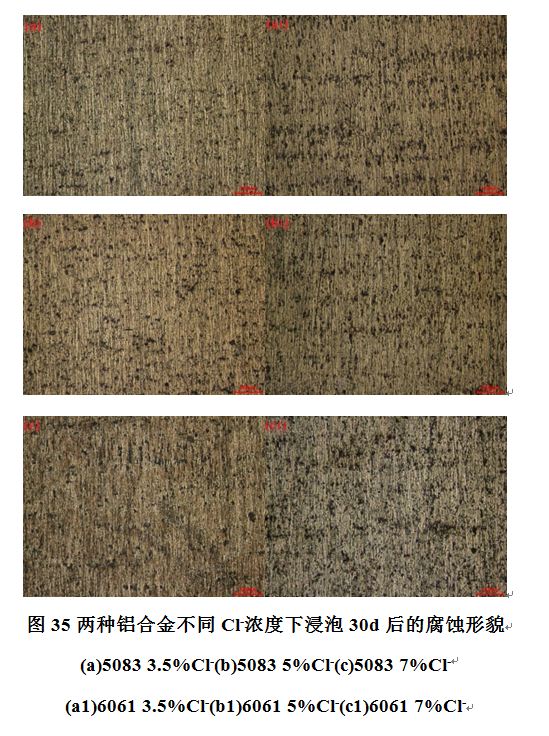
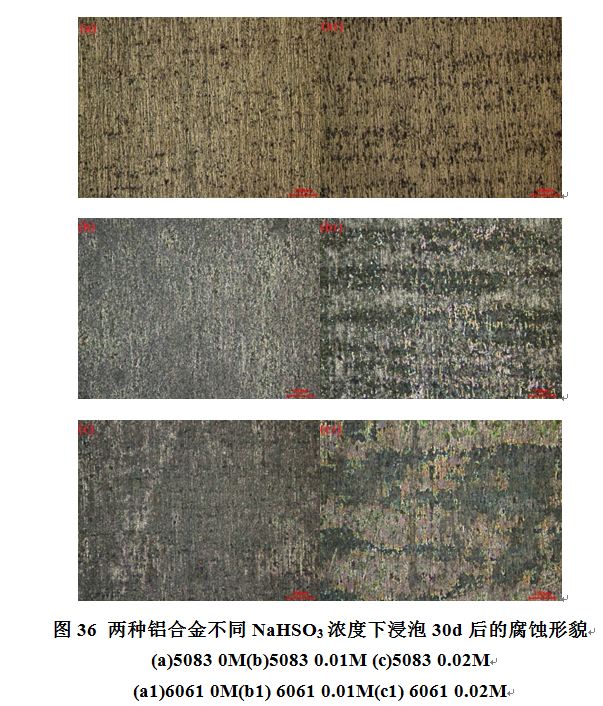
图37为两种铝合金不同溶液中浸泡30d后腐蚀产物的微观形貌,由图(a)可以看出5083-H116铝合金在3.5%NaCl溶液中浸泡30d后,表面有少量的白色团状腐蚀产物,未发生明显的腐蚀现象;由图(a1)可以看出,6061-T6铝合金在3.5%NaCl溶液中浸泡30d后,表面有较多白色腐蚀产物。图(b)可看出5083-H116铝合金在 0.01M NaHSO3+3.5%NaCl溶液中浸泡30d后,表面腐蚀产物在内应力作用下发生明显的龟裂现象,呈块状,并伴有腐蚀坑的产生;图(b1)可以看出 6061-T6铝合金在 0.01M NaHSO3+3.5%NaCl溶液中浸泡30d后,表面腐蚀产物也发生了明显的龟裂现象,但这种龟裂密度要比5083-H116铝合金大一些;疏松的腐蚀产物使腐蚀介质容易通过裂缝达到基体,使材料继续腐蚀。图(c)和图(c1)分别为5083和6061-T6铝合金在45℃的3.5%NaCl溶液中浸泡30d后的微观形貌,可以看出5083-H116铝合金表面分布着少量白色团状腐蚀产物,6061-T6铝合金的白色腐蚀产物要比5083-H116铝合金多一些,由放大图可以看出两种铝合金表面状态均为细密的针状组织,但5083-H116铝合金的表面致密性要比6061-T6铝合金高一些。
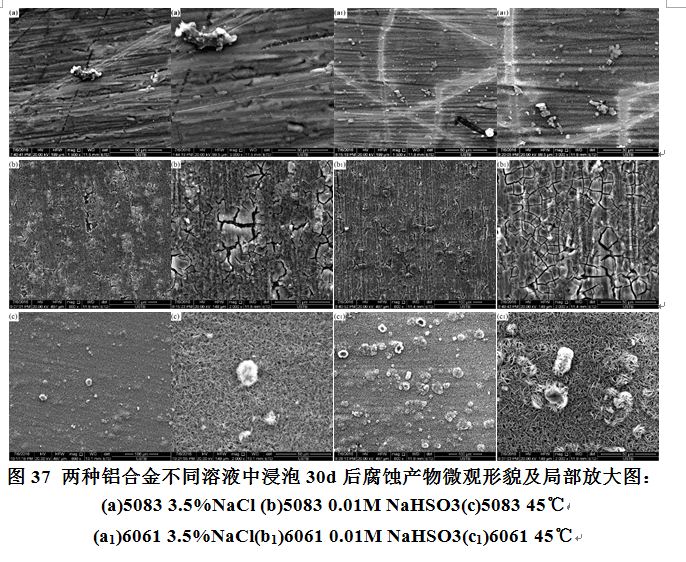
参考文献
[1] 罗雪, 李小强, 董重里. 腐蚀产物对6061铝合金海洋大气腐蚀过程的影响[J]. 腐蚀与防护, 2018, 039(008):587-591.
[2] 罗兰, 王一临. 盐雾试验方法探讨[J]. 装备环境工程, 2011, 8(4):77-81.
[3] 方晓祖, 曹学军, 闫薇,等. 7A52铝合金海洋大气环境试验与室内加速试验的相关性研究[J]. 环境工程, 2015(S1):358-361.
[4] 刘明, 蔡健平, 张晓云,等. 2A12铝合金模拟海洋大气腐蚀的加速试验研究[J]. 材料工程, 2010(z1):348-351,376.
[5] 杨浪, 赵起越, 贺建,等. 6061铝合金在模拟工业-海洋大气环境下的腐蚀研究[J]. 中国材料进展, 2018, 037(001):028-34.
[6] 郭晓军, 杨晓鸿. 海洋飞溅区模拟实验装置[J]. 腐蚀与防护, 1999, 020(006):289-290.
[7] 张爱萍, 田冰, 何其平. 一种耐候钢飞溅腐蚀试验装置: 中国, CN 2938075Y[P]. 2007.
[8] Li X , Bailey S I . A Laboratory Technique for Evaluating Marine Splash Zone Corrosion[J]. Advanced Materials Research, 2012, 347-353:3345-3350.
[9] 侯健, 郭为民, 王均涛. 一种海洋飞溅环境模拟试验装置: 中国, CN 102680385A[P]. 2012.
[10] 吴俊升,李晓刚,董超芳.一种海洋腐蚀模拟加速试验装置:中国,CN 101482482A[P].2009.
[11] 张展,许志龙,孙金娥,等.船用铝合金在模拟工业污染海洋环境中的腐蚀行为[J]. 材料保护,2019(12).
[12] 穆鑫, 魏洁, 董俊华, 等. 低碳钢在模拟海洋潮差区的腐蚀行为的电化学研究[J]. 金属学报, 2012, 48(004):420-426.
[13] 韩东锐, 张波, 欧家才, 等. 微弧氧化铝合金在海水中的腐蚀行为[J]. 腐蚀与防护, 2010, 31(006):452-454.
[14] 彭文才, 侯健, 郭为民, 等. 温度和溶解氧对5083铝合金海水腐蚀性的影响[J]. 装备环境工程, 2010, 007(003):22-26.
[15] 王勇, 迟骋远, 孙丽丽,等. 7005铝合金在模拟海水介质中的腐蚀行为研究[J]. 化工机械, 2019, 046(003):271-274.
[16] 刘雪琴. 模拟动态海水中高镁铝合金(5383)腐蚀行为及其机理研究[D].