- 专题资料:
- 北京科技大学
- 山东南山铝业股份有限公司
- 专题制作:
- 国家材料环境腐蚀平台
联系我们
-
-
电话: 010-62313558-802 -
地址: 北京市海淀区学院路30号 -
邮编: 100083
首页 > 舰船和海洋工程用铝合金金属腐蚀专题 > 腐蚀行为
船用铝合金腐蚀行为-外场暴露研究
1 船用铝合金在海洋大气中的腐蚀行为
户外大气暴露试验是研究大气腐蚀性最直接的试验方式,试验结果最接近实际情况,效果良好。研究人员在海南万宁试验站开展了7年的环境试验,积累了7A52铝合金在万宁海洋大气环境下的暴露试验数据,得到了7A52铝合金的海洋大气环境腐蚀失重曲线[1]。苏艳等[2]开展了海南试验站海洋平台户外大气暴露和棚下大气暴露试验,研究了高强铝合金在海洋大气环境下的剥层腐蚀机理。但户外大气暴露试验周期长,同时外场试验存在较多不便,且需要消耗较多资源,存在一定程度的局限性。
1.1 铝合金泰国曼谷暴露腐蚀行为研究
本节通过在泰国曼谷地区对5083铝合金进行为期1年的暴晒试验,研究了泰国曼谷的海洋大气环境下铝合金的腐蚀行为。
1.1.1 泰国曼谷大气暴晒实验方法
实验材料为5083铝合金,主要成分见表1,采用电子背散射衍射(EBSD)对铝合金微观组织进行表征,实验结果见图1,将材料制成150×75×3mm的大气投放试样,经过车铣、打孔标记、打磨、除污清洗及干燥,使用精度为0.0001g分析天平称量原始重量并记录,之后在泰国曼谷进行为期1年的暴晒实验。
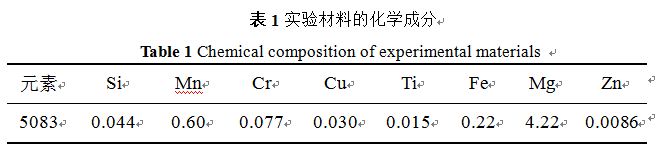
将暴晒1年后的5083铝合金试样回收,采用数码相机和激光共聚焦对试样表面腐蚀形貌进行拍照观察,利用Quanta-250环境扫描电镜对铝合金表面及截面微观形貌进行观察及能谱分析;按照GB/T16545-1996使用硝酸溶液对试样表面腐蚀产物进行清除,清洗干燥后称重,计算在泰国曼谷暴晒一年后的腐蚀速率。
1.1.2 泰国曼谷大气暴晒腐蚀形貌分析
5083铝合金在泰国曼谷暴晒一年后的腐蚀形貌如图2所示,由宏观形貌可知,试样表面附着较多尘埃颗粒物,未出现明显的锈蚀,具有明显的金属光泽,微观形貌可知,5083铝合金含有较多的Mg、Si、Fe等耐蚀元素,表面氧化膜较为致密[11],仅在局部发生点蚀,点蚀坑大小约为5-30μm。
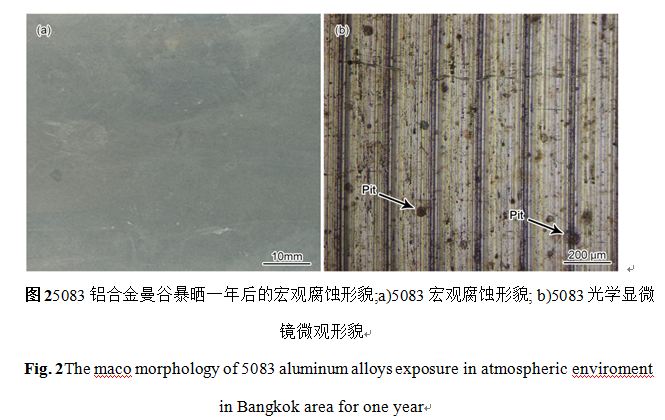
为了研究5083铝合金泰国曼谷暴晒一年后的微观腐蚀形貌,采用Quanta250扫描电镜对铝合金微观腐蚀形貌及截面形貌进行观察,实验结果如图3所示,由此可知,铝合金表面出现明显的圆状点蚀坑,5083铝合金表面分布约50μm点蚀坑,腐蚀产物层厚约为2-3μm,由于加入Mg元素,提高了表面钝化膜的形成能力,腐蚀产物较为致密。

1.1.3 泰国曼谷大气暴晒腐蚀速率
按照GB/T16545-1996用硝酸溶液去除表面腐蚀产物,之后酒精清洗、干燥后称量。按照公式(1)计算腐蚀失重速率。
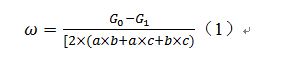
其中,ω为腐蚀失重速率,g•m-2•y-1;G0为试样原始重量,g;G1为去除腐蚀产物后重量,g;a、b、c为试样长度、宽度、厚度,m。5083含有较多Mg、Si、Fe等耐蚀元素,腐蚀速率相对较小,约为0.7g.m-2.y-1。
1.1.4 泰国曼谷大气暴晒电化学实验
为了研究5083铝合金在大气环境中的腐蚀机理,使用输力强电化学工作站测试泰国曼谷大气环境中暴晒1年后5083铝合金在0.1M NaCl溶液中的极化曲线和电化学阻抗谱,极化曲线结果如图4所示,由此可知,5083铝合金腐蚀电位约为-0.68 VSCE,腐蚀电流约为1.62×10-7A.cm-2,极化曲线没有明显的钝化区间[12]。
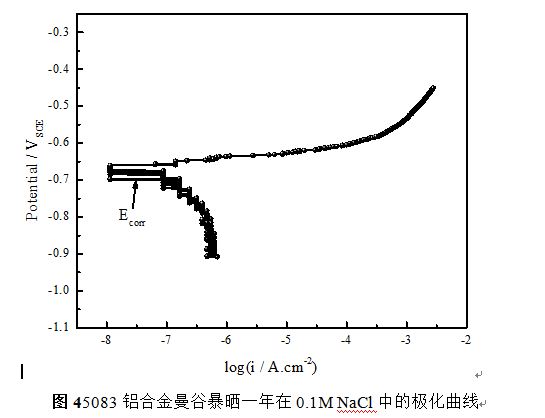
电化学阻抗谱实验结果如图5所示,通过ZSimpwin软件拟合等效电路如图6所示,其中Re为溶液电阻,CPE1为工作电极表面的双电层电容,R1为工作电极表面反应的电荷转移电阻,CPE2为腐蚀产物层或钝化膜电容,R2为电极表面腐蚀产物层或钝化膜电阻[13],各元件参数值见表2,5083铝合金钝化膜电阻约为2.249×106Ω.cm2[14-15]。
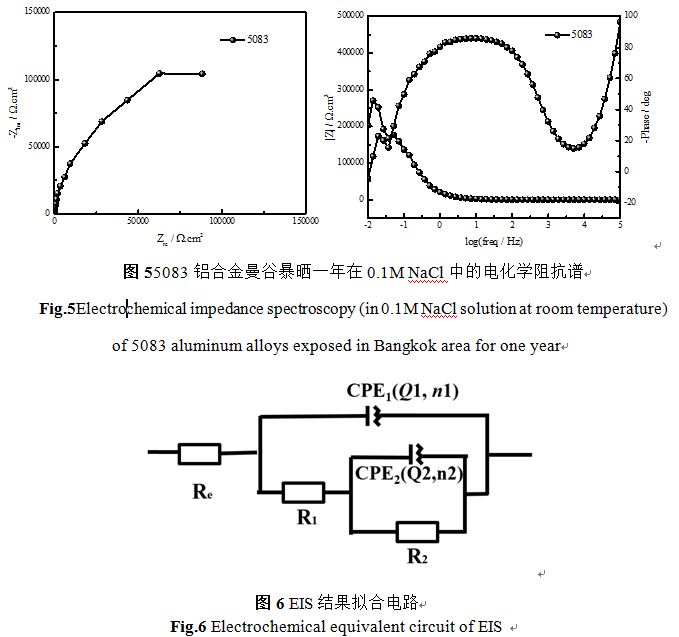
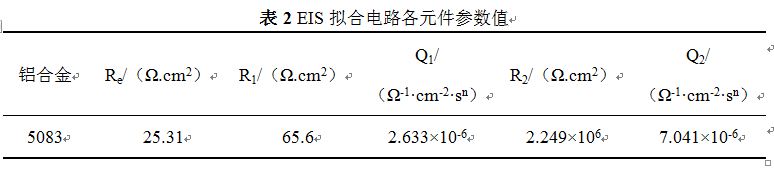
2 船用铝合金在海水中的腐蚀行为
在实际海域的海水暴露试验是研究海水不同区域腐蚀作用最直接有效的方式。常彦衍等[9]在厦门海域的全浸区和潮差区进行了LY12CZ的挂片腐蚀试验,并将腐蚀与气象环境因素进行了相关度分析与排序。黄桂桥[10-12]在青岛海域海水的飞溅区、潮汐区和全浸区分别开展了工业纯铝L4M 、锻铝LD2CS等十余种铝合金长达16年的暴露腐蚀试验,研究了不同铝合金在不同海洋环境中的耐蚀性。但实际海水暴露试验受户外试验场条件的制约,试验研究存在诸多不便,耗时耗力,同样具有局限性。
2.1 船用铝合金中国南海深海环境腐蚀行为研究
本节通过实海暴露实验,研究了5052和6061铝合金在中国南海海域800 m和1200 m深海环境下浸泡的腐蚀行为[13]。
2.1.1 南海深海环境腐蚀实验方法
完成5052和6061铝合金在我国南海海域进行深海腐蚀试验装置的投放工作,时间为3a。投放深度分别为800和1200m,暴露地点的海水环境因素列于表3中。
投放试样的长边垂直于板材轧制方向.试样投放前进行去油处理,并对试样尺寸和重量进行精确测量并记录。暴露实验结束后,将试样取回,酸洗去除腐蚀产物。酸洗液按照GB/T 16545-1996配置。进行样品宏观腐蚀形貌观察分析。进行微观腐蚀形貌观察并分析腐蚀产物的成分及相组成。并采用GB/T 18590-2001中的显微法测量评定点蚀坑的深度。
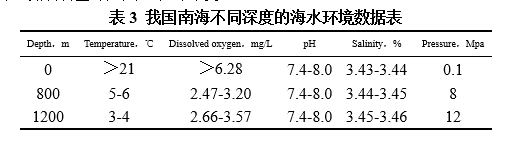
2.1.2 南海深海环境腐蚀速率分析
5052和6061铝合金在南海800和1200 m暴露3a的平均腐蚀速率和最大点蚀坑深度如图7示。可以看出,5052和6061铝合金在南海1200m环境下的平均腐蚀速率(0.026和0.068mm/a)均低于在800m环境下的平均腐蚀速率(0.044和0.069mm/a)。比较2种铝合金的平均腐蚀速率发现,5052铝合金的平均腐蚀速率远低于6061铝合金。由于铝合金在深海环境下主要发生的是点腐蚀,因此,最大点蚀坑深度更能反映材料的耐腐蚀性能从图7中的最大点蚀坑深度数据可知,相较于800m深海环境(1.097和3.820 mm),5052和6061铝合金在1200m深海下的最大点蚀坑深度(0.496和2.242mm)大幅下降。5052铝合金的最大点蚀坑深度也远小于6061铝合金。其中,6061铝合金在南海800m深海环境下浸泡3a后已经发生了点蚀穿孔。
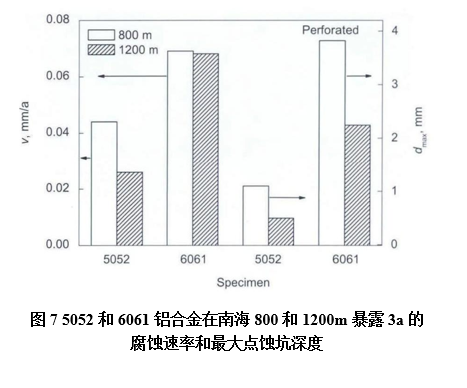
2.1.3 南海深海环境腐蚀形貌分析
图8为5052和6061铝合金在南海800和1200 m实海暴露3a后表面腐蚀的宏观照片。可以看出,2种铝合金在深海环境下均发生了很严重的局部腐蚀,表面形成了白色的腐蚀产物。在铆接区域发生了严重的缝隙腐蚀,造成穿孔。在样品其它区域发生了点腐蚀,其中6061铝合金表面的点蚀坑直径更大,密度更高。图9为5052和6061铝合金去除腐蚀产物后的宏观形貌,图中圆圈标出的位置为缝隙腐蚀或点腐蚀造成的穿孔位置。5052铝合金在铆接处发生了严重的缝隙腐蚀,并造成大面积穿孔。6061铝合金在铆接处也发生了缝隙腐蚀,并造成局部穿孔。在样品主表面,5052铝合金在800 m深海环境下多处产生溃疡状腐蚀坑,而在1200 m深海环境下的点腐蚀较轻微。在样品主表面,6061铝合金主要发生的是点腐蚀,其中,在800 m深海环境下生成的点蚀坑的密度虽然没有在1200 m深海环境下的高,但是点蚀坑的深度更大,甚至在多处出现了局部腐蚀穿孔。将深海环境中的腐蚀特征和浅海的腐蚀特征相比,可知5052和6061铝合金在深海环境下的局部腐蚀类型与在浅海中的相同,均为缝隙腐蚀和点腐蚀,但深海环境中的腐蚀更严重。
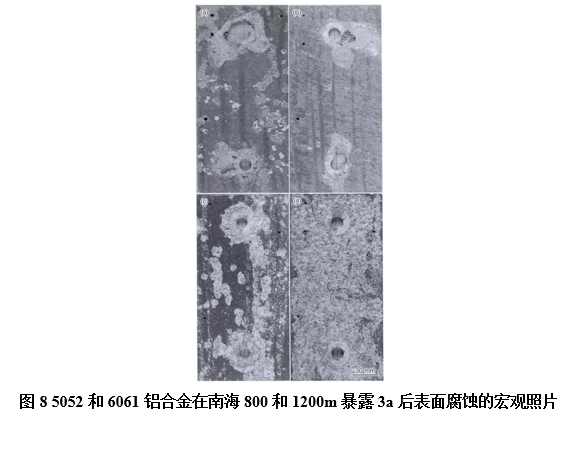
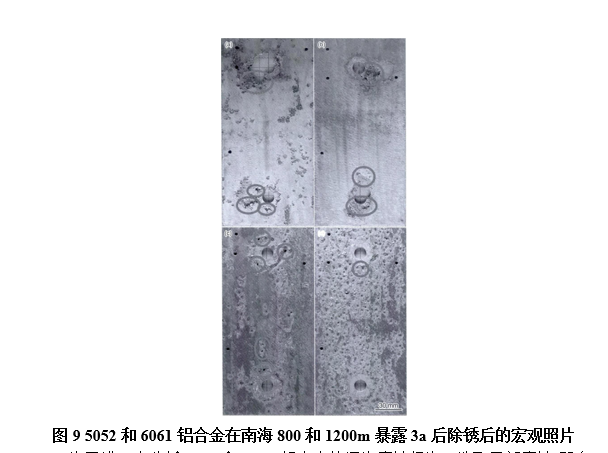
为了进一步分析5052和6061铝合金的深海腐蚀行为,选取局部腐蚀(即白色腐蚀产物堆积处)区域进行了腐蚀微观形貌观察,如图10所示。5052铝合金在800 m深海下形成的腐蚀产物不规则地堆积在溃疡状腐蚀坑处,而5052铝合金在1200 m深海下表面几乎没有腐蚀产物附着。6061铝合金在深海环境下形成的腐蚀产物聚集在点蚀坑底,腐蚀产物疏松,且有裂纹。
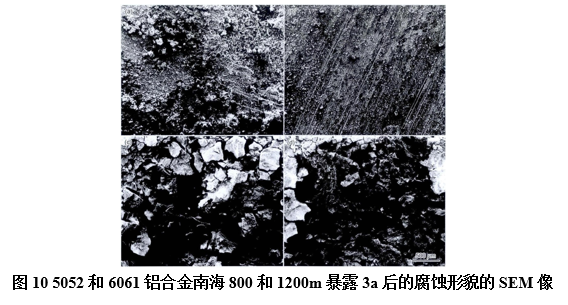
2.1.4 南海深海环境腐蚀产物分析
图11为5052和6061铝合金在南海800和1200m实海暴露3a后的腐蚀产物EDS结果,由图可知,2种铝合金表面的腐蚀产物主要由Al和O组成,还含有少量的Si,Mg,Na,S和Cl。具体的元素含量列于表4中。图12为5052和6061铝合金在南海800和1200m实海暴露3a后的腐蚀产物的XRD谱。结合EDS分析结果可知,腐蚀产物由Al2O3,SiO2,以及少量Mg3(SO4)2(OH)2和NaCl组成。
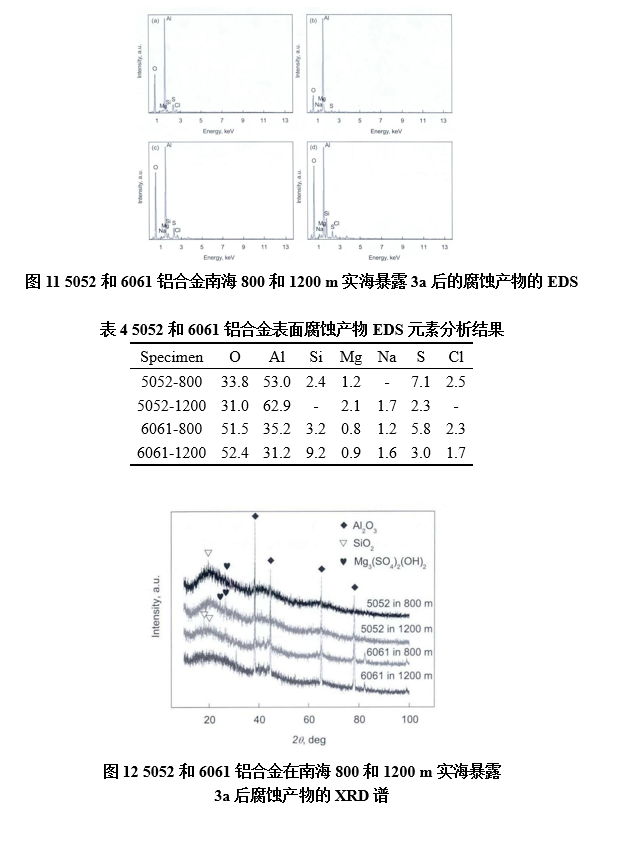
参考文献
[1] 方晓祖, 曹学军, 闫薇,等. 7A52铝合金海洋大气环境试验与室内加速试验的相关性研究[J]. 环境工程, 2015(S1):358-361.
[2] 苏艳, 李凌杰, 舒畅,等. 高强铝合金海洋大气环境剥层腐蚀研究[C]// 全国环境试验技术学术研讨会. 2010.
[3] 王力, 董超芳, 张达威,等. 合金元素对铝合金在泰国曼谷地区初期腐蚀行为的影响[J]. 金属学报, 2019, 56(1):119-128.
[4] 郑传波, 李春岭, 益帼,等. 高强铝合金6061和7075在模拟海洋大气环境中的腐蚀行为[J].材料保护,2014,47(06):38.
[5] SUO X N, GUO C, KONG D C, et al. Corrosion behaviour of TiN and CrN coatings produced by magnetron sputtering process on aluminium alloy[J]. Int. J. Electrochem. Sci., 2019,14:826
[6] Chen M A , Ou Y C , Fu Y H , et al. Effect of friction stirred Al-Fe-Si particles in 6061 aluminum alloy on structure and corrosion performance of MAO coating[J]. Surface and Coatings Technology, 2016, 304:85
[7] Chung I C , Chung C K , Su Y K . Effect of current density and concentration on microstructure and corrosion behavior of 6061 Al alloy in sulfuric acid[J]. Surface & Coatings Technology, 2017, 313:299
[8] Nejadseyfi O , Shokuhfar A , Dabiri A , et al. Combining equal-channel angular pressing and heat treatment to obtain enhanced corrosion resistance in 6061 aluminum alloy[J]. Journal of Alloys and Compounds, 2015, 648:912
[9] 常彦衍, 张峥. LY12CZ厦门海域全浸区和潮差区腐蚀结果分析[J]. 材料工程, 2004(4):37-39.
[10] 黄桂桥.铝合金在海洋环境中的腐蚀研究(Ⅰ)——海水潮汐区16年暴露试验总结[J].腐蚀与防护,2002(01):18-20+23.
[11] 黄桂桥.铝合金在海洋环境中的腐蚀研究(Ⅱ)——海水全浸区16年暴露试验总结[J].腐蚀与防护,2002(02):47-50.
[12] 黄桂桥. 铝合金在海洋环境中的腐蚀研究(Ⅲ)——海水飞溅区16年暴露试验总结[J]. 腐蚀与防护, 2003, 24(002):47-50.
[13] 孙飞龙, 李晓刚, 卢琳,等. 5052和6061铝合金在中国南海深海环境下的腐蚀行为研究[J]. 金属学报, 2013, 49(10):1219-1226.
[1]HUANG B Y, LI C G, SHI L K, et al. Non-ferrous metal materials manual (I) [M]. Beijing: Chemical Industry Press, 2009: 109. (黄伯云, 李成功, 石开力, 邱冠周, 左铁镛. 有色金属材料手册(上)[M]. 北京: 化学工业出版社, 2009: 109.) [2]Yasakau, K. A. Zheludkevich, M. L.; Ferreira, M. G. S., Role of intermetallics in corrosion of aluminum alloys[J]. Smart corrosion protection. 2018, 425-462. [3] LIU Y J, WANG Z Y, KE W, et al.Corrosion behavior of 2024-T3 aluminum alloy in simulated marine atmospheric environment[J]. The Chinese Journal of Nonferrous Metals.2013,5:1208. (刘艳洁, 王振尧, 柯伟. 2024-T3铝合金在模拟海洋大气环境中的腐蚀行为[J]. 中国有色金属学报, 2013(5):1208-1216.) [4] XIAO Y D, Wang G Y, Li X G, et al. The Corrosive Characteristics of Atmospheric Environment and Materials in WesternChina [J]. J. Chin. Soc. Corros. Prot., 2003, (4): 57. (萧以德,王光雍,李晓刚等. 我国西部地区大气环境腐蚀性及材料腐蚀特征[J].中国腐蚀与防护学报,2003,(4):5) [5] WANG L, GUO C Y, XIAO K, et al. Corrosion behavior of carbon steels Q235 and Q450 in dry hot atmosphere at Turpan district for four years[J]. Journal of Chinese Society for Corrosion and Protection, 2018, 38:431 (王力,郭春云,肖葵等. Q235和Q450钢在吐鲁番干热大气环境中长周期暴晒时的腐蚀行为研究[J]. 中国腐蚀与防护学报, 2018,38:431.) [6] GAO M, SUN Z H, LIU M, et al.Atmospheric Corrosion Behavior of 7B04 Aluminum Alloy in the presence of NaCl and SO2[J].Environmental Testing,2016,34:9 (高蒙,孙志华,刘明,闫巍,汤智慧.7B04铝合金在NaCl沉积与SO_2环境下的大气腐蚀行为[J].环境技术,2016,34(05):9.) [7] ZHUO H R, LI X G, DONG C F. Review of atmospheric corrosion behavior and mechanism of aluminum alloys and it’s anodic film[J]. Equipment Environmental Engineering,2006,1 (周和荣,李晓刚,董超芳.铝合金及其氧化膜大气腐蚀行为与机理研究进展[J].装备环境工程,2006,1) [8]L.E. Fratila-Apachitei, H. Terryn, P. Skeldon, et al.Influence of substrate microstructure on the growth of anodic oxide layers[J].Electrochimica Acta,2004,49:1127 [9] WANG B B, WANG Z Y, CAO G W, et al. Localized corrosion of aluminum alloys 2024 exposed to salt lake atmospheric environment in western China[J].Acta Metallurgica Sinica, 2014,50:49 王彬彬,王振尧,曹公望,刘艳洁,柯伟.2024铝合金在中国西部盐湖大气环境中的局部腐蚀行为[J].金属学报,2014,50(01):49. [10]Wei X, Dong C F, Chen Z H, et al. A DFT study of the adsorption of O2 and H2O on Al(111) surfaces[J].Rsc Advances, 2016, 6:56303. [11]ZHENG C B, LI C L, YI J, et al.Corrosion behavior of high-strength aluminum alloys 6061 and 7075 in simulated marine atmosphere [J].Materials Protection, 2014, 47:38. (郑传波,李春岭,益帼等.高强铝合金6061和7075在模拟海洋大气环境中的腐蚀行为[J].材料保护,2014,47(06):38.) [12] SUO X N, GUO C, KONG D C, et al.Corrosion behaviour of TiN and CrN coatings produced by magnetron sputtering process on aluminium alloy[J].Int. J. Electrochem. Sci., 2019,14:826 [13]Chen M A , Ou Y C , Fu Y H , et al. Effect of friction stirred Al-Fe-Si particles in 6061 aluminum alloy on structure and corrosion performance of MAO coating[J]. Surface and Coatings Technology, 2016, 304:85 [14]Chung I C , Chung C K , Su Y K . Effect of current density and concentration on microstructure and corrosion behavior of 6061 Al alloy in sulfuric acid[J]. Surface & Coatings Technology, 2017, 313:299 [15]Nejadseyfi O , Shokuhfar A , Dabiri A , et al. Combining equal-channel angular pressing and heat treatment to obtain enhanced corrosion resistance in 6061 aluminum alloy[J]. Journal of Alloys and Compounds, 2015, 648:912 [16] Miera M S D , Curioni M , Skeldon P , et al. The behaviour of second phase particles during anodizing of aluminium alloys[J]. Corrosion Science, 2010, 52(7):2489 [17]Huang L P, Chen K H, Li S. Influence of grain-boundary pre-precipitation and corrosion characteristics of inter-granular phases on corrosion behaviors of an Al–Zn–Mg–Cu alloy[J]. Materials Science & Engineering B, 2012, 177(11):862 [18] MAN C, DONG C F, XIAO K, et al. The combined effects of chemical and structural factors on pitting corrosion induced by MnS-(Cr,Mn,Al)O duplex inclusions[J].Corrosion,2018,74:312 [19] Tanem B S, Svenningsen G, MaRdalen J. Relations between sample preparation and SKPFM Volta potential maps on an EN AW-6005 aluminium alloy[J]. Corrosion Science, 2005, 47(6):1506 [20] Esfahani Z , Rahimi E , Sarvghad M , et al. Correlation between the histogram and power spectral density analysis of AFM and SKPFM images in an AA7023/AA5083 FSW joint[J]. Journal of Alloys and Compounds, 2018,744:174. [21] Ornek, C, Engelberg D L. SKPFM Measured Volta Potential Correlated with Strain Localisation in Microstructure to Understand Corrosion Susceptibility of Cold-rolled Grade 2205 Duplex Stainless Steel[J]. Corrosion Science, 2015, 99:164